As the demand for clean, renewable energy grows, offshore wind farms have emerged as a promising solution. However, maintaining these towering turbines in the harsh marine environment presents unique challenges. From corrosion and extreme weather to accessibility issues, offshore wind turbine maintenance requires innovative strategies and cutting-edge technologies to ensure optimal performance and longevity.
In this article, we will dive deep into the world of offshore wind turbine maintenance, exploring the preventive and predictive techniques used to keep these engineering marvels spinning smoothly. We will also showcase real-world examples and case studies of successful maintenance practices from around the globe, highlighting the ingenuity and dedication of the professionals who keep these clean energy powerhouses running.
Join us as we unravel the complexities of offshore wind turbine maintenance and discover the groundbreaking solutions that are shaping the future of sustainable energy. Get ready to be inspired by the incredible potential of offshore wind and the unsung heroes who work tirelessly to harness its power for a greener tomorrow.
Unique Challenges of Offshore Wind Turbine Maintenance
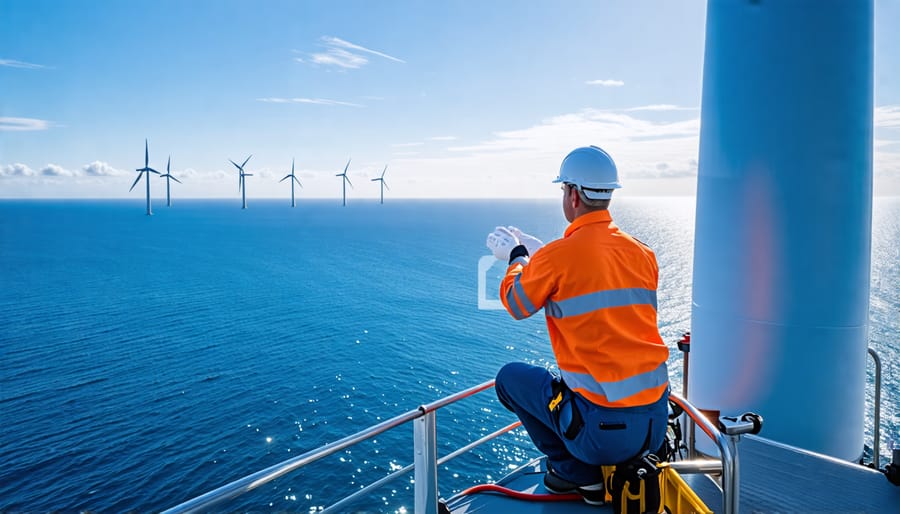
Corrosion and Weather Damage
The harsh marine environment poses significant challenges for offshore wind turbines, as they are constantly exposed to saltwater, high winds, and severe storms. Saltwater can accelerate corrosion on turbine components, particularly on metal parts such as towers, nacelles, and blades. This corrosion weakens the structural integrity of the turbine, leading to reduced efficiency and potential failures. High winds and storms also take a toll on turbines, subjecting them to intense forces that can cause damage to blades, gearboxes, and other critical components. Over time, this weather-related wear and tear can result in decreased performance, increased maintenance requirements, and shorter lifespans for offshore wind turbines. To mitigate these issues, manufacturers use specialized coatings, galvanization, and cathodic protection to enhance the corrosion resistance of turbine parts. Regular inspections and preventive maintenance are also crucial to identify and address any weather-related damage before it escalates into more serious problems.
Access and Logistics
Accessing offshore wind turbines for maintenance poses unique logistical challenges due to their remote locations. Specialized vessels, such as crew transfer vessels (CTVs) and service operation vessels (SOVs), are required to transport technicians and equipment safely to the turbines. These vessels must be capable of operating in various weather conditions and provide a stable platform for maintenance activities. Helicopter transfers are sometimes used in extreme cases, but they are costly and limited by weather conditions.
Offshore wind farms are often located far from shore, requiring careful planning and coordination to ensure efficient maintenance operations. Weather windows, tidal patterns, and sea state conditions must be considered when scheduling maintenance tasks. Technicians may need to stay on-site for extended periods, necessitating the provision of living quarters and amenities on SOVs. Despite these challenges, advancements in vessel design and technology are improving access and logistics, making offshore wind turbine maintenance more efficient and cost-effective.
Height and Scale
Offshore wind turbines are among the largest man-made structures, with some reaching heights of over 850 feet (260 meters) and blade spans exceeding 500 feet (150 meters). These colossal dimensions pose unique challenges for maintenance crews, who must navigate the towering heights and contend with the harsh marine environment. Specialized equipment, such as jack-up vessels and custom-built cranes, is required to access and repair these gigantic turbines. The sheer scale of the components, including massive blades and heavy nacelles, demands meticulous planning and execution to ensure safe and efficient maintenance operations. Despite the challenges, the immense size of offshore wind turbines is a testament to the incredible engineering feats achieved in the pursuit of clean, renewable energy.
Preventive Maintenance Strategies
Preventive maintenance is the backbone of offshore wind turbine reliability and performance. By proactively addressing potential issues before they escalate, operators can minimize downtime, extend equipment lifespan, and optimize energy output. Regular inspections and servicing are crucial in the harsh marine environment, where components are exposed to salt spray, high winds, and wave action.
Key preventive maintenance tasks include lubricating bearings, replacing filters, and checking blade integrity. Technicians use specialized equipment, such as drones and remote-operated vehicles (ROVs), to safely access turbines and perform visual inspections. They look for signs of corrosion, damage, or wear on critical components like gearboxes, generators, and foundations.
Preventive maintenance schedules are tailored to each wind farm’s unique conditions and turbine models. Typically, minor inspections occur every few months, with more comprehensive servicing annually or semi-annually. During these visits, technicians perform tasks such as oil changes, bolt tightening, and calibration of sensors and control systems.
Effective preventive maintenance relies on data-driven insights. Operators monitor turbine performance metrics, such as power output, vibration levels, and temperature, to identify trends and anomalies. This information helps optimize maintenance intervals and catch potential issues early.
Investing in preventive maintenance not only improves reliability but also reduces overall costs. By preventing major failures and unplanned downtime, operators minimize lost revenue and expensive repairs. Proactive care also extends the operational lifetime of offshore wind assets, ensuring a better return on investment.
As the offshore wind industry continues to grow, best practices in preventive maintenance will evolve. Collaboration among operators, sharing of data and experiences, and adoption of innovative technologies will be key to driving efficiency and sustainability in this critical area of offshore wind turbine management.
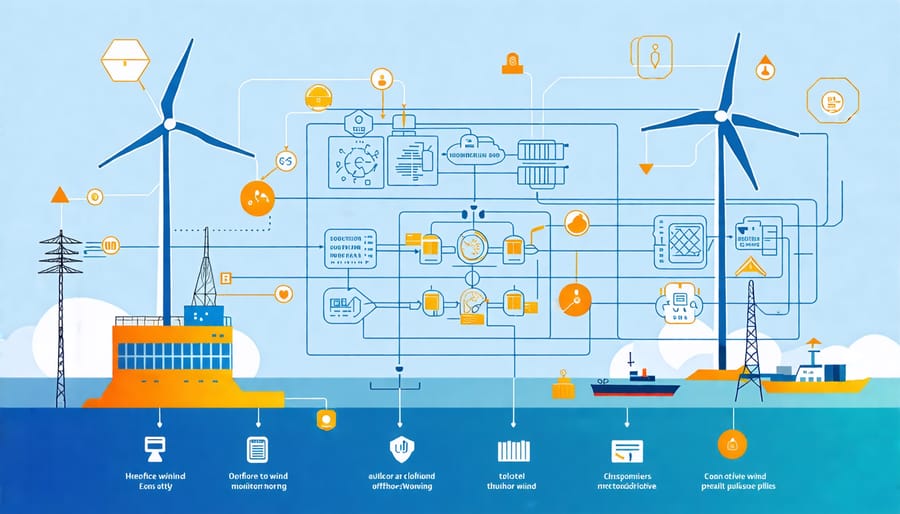
Predictive Maintenance and Condition Monitoring
Vibration Analysis
Vibration analysis is a powerful predictive maintenance technique that helps detect potential issues in offshore wind turbines before they lead to costly downtime. By using specialized sensors to monitor the vibration patterns of critical components like bearings, gearboxes, and shafts, maintenance teams can identify early signs of wear, imbalances, misalignments, or other mechanical problems. Advanced software algorithms analyze the collected vibration data, comparing it to baseline readings and known fault patterns to pinpoint the source and severity of any anomalies. This allows for targeted maintenance interventions, such as bearing replacements or balancing adjustments, to be scheduled during planned downtime, minimizing disruption to energy production. Vibration analysis not only helps extend the lifespan of wind turbine components but also optimizes overall system performance and reliability. As offshore wind farms continue to expand, this predictive maintenance approach will play an increasingly crucial role in ensuring their long-term success and contribution to a sustainable energy future.
Oil Analysis
Oil analysis is a powerful diagnostic tool for offshore wind turbine maintenance. By examining oil samples from critical components like gearboxes and bearings, technicians can detect contaminants such as metal particles, water, or dirt that may indicate wear or damage. Spectrographic analysis reveals the presence and concentration of wear metals, allowing for early identification of component degradation before failures occur. Regular oil sampling and analysis help establish baseline data and monitor trends over time, enabling predictive maintenance strategies. This proactive approach reduces unplanned downtime, extends component life, and optimizes overall wind turbine performance in the challenging marine environment.
Thermal Imaging
Infrared cameras have become an essential tool in offshore wind turbine maintenance, allowing technicians to detect electrical hotspots and overheating components without the need for physical contact. By capturing thermal images of the turbine’s internal systems, these cameras can identify areas of excessive heat, which often indicate potential faults or malfunctions. This non-invasive method enables maintenance crews to pinpoint issues quickly and accurately, reducing downtime and preventing costly repairs. Thermal imaging is particularly useful for inspecting electrical connections, bearings, and gearboxes, as these components are prone to heat-related issues. Regular thermal inspections can help detect problems early on, allowing for timely interventions and minimizing the risk of severe damage or failure. As offshore wind farms continue to expand, the use of thermal imaging technology will play an increasingly crucial role in ensuring the efficient and reliable operation of these sustainable energy systems.
Innovations in Offshore Wind Maintenance
The offshore wind industry is witnessing a surge of innovative technologies and techniques aimed at streamlining maintenance processes and enhancing safety. One groundbreaking development is the use of drones for inspections. Equipped with high-resolution cameras and advanced sensors, these unmanned aerial vehicles can quickly and efficiently assess the condition of wind turbine blades, towers, and other components. By eliminating the need for human technicians to physically access hard-to-reach areas, drones significantly reduce the risk of accidents and the time required for inspections.
Another cutting-edge solution is the implementation of robotic systems for maintenance tasks. Crawling robots, such as those developed by BladeBUG, can navigate the surface of wind turbine blades, performing detailed inspections and even carrying out minor repairs. These robots are equipped with advanced imaging technology and can operate in challenging weather conditions, minimizing downtime and improving overall efficiency.
Predictive maintenance powered by artificial intelligence (AI) is also gaining traction in the offshore wind sector. By analyzing vast amounts of data collected from sensors installed on wind turbines, AI algorithms can identify potential issues before they escalate into costly failures. This proactive approach allows maintenance teams to schedule repairs during optimal weather windows, reducing the impact on energy production.
Furthermore, the use of virtual and augmented reality (VR/AR) is revolutionizing training and remote collaboration in offshore wind maintenance. VR simulations enable technicians to practice complex procedures in a safe, controlled environment, enhancing their skills and preparedness. AR technology, such as smart glasses, allows experts to remotely guide on-site technicians through repairs, minimizing the need for physical presence and reducing response times.
As the offshore wind industry continues to expand, the adoption of these innovative technologies and techniques will be crucial in ensuring the long-term reliability, efficiency, and cost-effectiveness of wind turbine maintenance. By embracing cutting-edge solutions, the sector can overcome the unique challenges posed by the harsh marine environment and pave the way for a sustainable energy future.
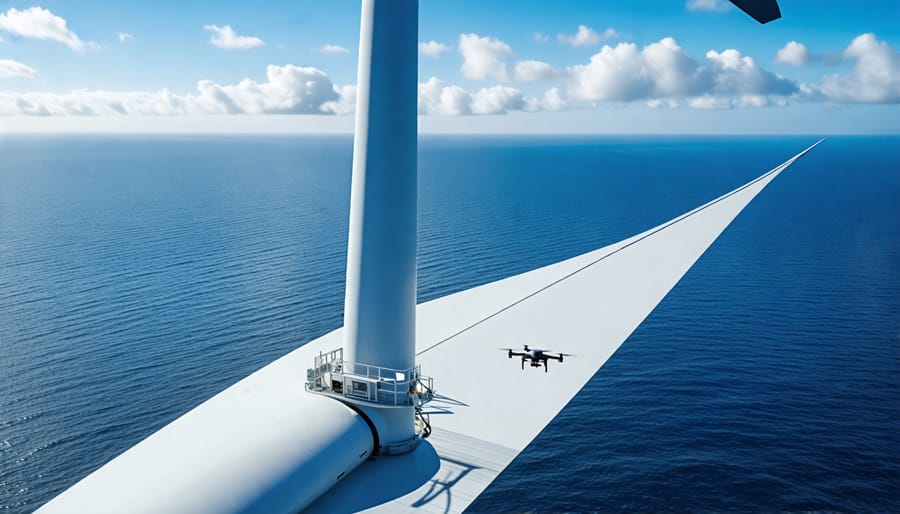
Conclusion
In conclusion, offshore wind turbine maintenance is a critical aspect of ensuring the long-term viability and success of this renewable energy source. By addressing the unique challenges posed by the harsh marine environment, implementing effective preventive and predictive maintenance strategies, and embracing innovative solutions like advanced sensors, AI, and drones, the industry can optimize the performance and lifespan of these powerful turbines. As technology continues to advance and best practices are refined, the future of offshore wind energy looks brighter than ever. With proper maintenance at the forefront, offshore wind will undoubtedly play a significant role in the global transition to a clean, sustainable energy future.